Case History: From 0 to 300, How Eastridge Helped a Manufacturer Rapidly Ramp Up Production
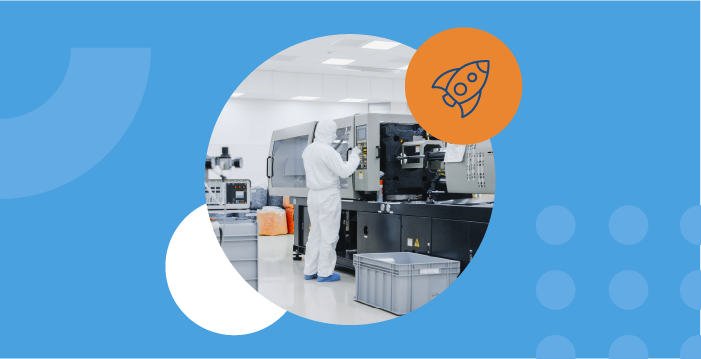
In the fast-paced world of diagnostic health technology and manufacturing, the ability to quickly scale up production is critical to a company’s success. Diagnostic manufacturers, especially those focused on providing accurate, point-of-care testing solutions, deal with the challenge of balancing rapid growth with stringent quality and regulatory requirements. When faced with increasing demand for its innovative blood testing products, one diagnostic manufacturer needed to expand its workforce from 0 to 300 employees in just a few months. By partnering with Eastridge Workforce Solutions, the company was able to meet its production goals while maintaining the highest standards of quality and operational efficiency.
This case study explores how Eastridge helped one diagnostic manufacturer ramp up its workforce and successfully navigate the complexities of rapid production growth.
The Challenge: Rapid Expansion with Limited Time
The manufacturer, a leader in diagnostic testing, faced an unexpected production boom due to increased demand for its point-of-care testing products. While the company had strong internal processes in place, its current workforce was insufficient to meet the production needs. The challenge was to hire 300 qualified employees in a short period of time without compromising on quality or disrupting the production line.
Several key obstacles had to be overcome:
- Limited time: The company needed to scale up its workforce within a few months to meet demand spikes.
- Qualified candidates: The roles required specific technical skills, which narrowed the pool of potential candidates.
- Operational disruption: The rapid expansion needed to occur without disrupting current production schedules or impacting product quality.
Facing these challenges, the company turned to Eastridge for assistance in building a scalable, high-quality workforce solution.
Step 1: Planning and Forecasting with Eastridge
The first step in the process was for Eastridge to sit down with the manufacturer’s leadership team and develop a comprehensive workforce plan. This involved analyzing production schedules, headcount requirements, and key milestones that needed to be met. Eastridge’s deep expertise in manufacturing allowed them to ask the right questions, such as:
- How many employees will be needed at each stage of production?
- What technical skills are required for these roles?
- What is the timeline for meeting production targets?
Through these conversations, Eastridge developed a detailed hiring roadmap that broke down the 300-employee headcount goal into manageable phases. By forecasting workforce needs and aligning recruitment efforts with production schedules, Eastridge ensured that the ramp-up process would be smooth and efficient.
Step 2: Leveraging the GATE Program to Qualify Candidates
To ensure the quality of hires during the rapid ramp-up, Eastridge implemented its GATE (Gateway to Attaining Technical Experience) program. This program is designed to bridge the skills gap by assessing candidates' technical abilities before they enter the workforce. Given the highly technical nature of the diagnostic manufacturing roles, the GATE program played a crucial role in ensuring that only the most qualified candidates were selected for the job.
Through hands-on evaluations and assessments focused on dexterity, the ability to follow SOPs, and adherence to GMP (Good Manufacturing Practice) guidelines, Eastridge could verify that candidates possessed the skills necessary to succeed in the production environment. This helped the manufacturer avoid hiring underqualified workers and ensured that new hires were capable of meeting the company’s high production and quality standards from day one.
This use of the GATE program not only improved candidate quality but also reduced turnover rates, as employees who demonstrated their technical abilities during the assessment phase were more likely to stay on the job and perform well.
Step 3: Building a Pipeline of Qualified Candidates
One of the biggest challenges the manufacturer faced was finding candidates with the right technical skills to work on the production line. These positions required specific expertise in handling equipment, following Standard Operating Procedures (SOPs), and meeting production quotas.
Eastridge leveraged its extensive candidate pipeline and recruitment network to source individuals who met these criteria. Using targeted recruitment strategies, Eastridge focused on identifying candidates with:
- Technical expertise: The ability to operate machinery and follow detailed instructions.
- Reliability and work ethic: A track record of dependability and the willingness to meet production deadlines.
- Flexibility: The capacity to quickly adapt to the fast-paced environment of a rapidly growing company.
By tapping into its established network of candidates and enhancing the selection process with the GATE program, Eastridge was able to quickly build a talent pool that aligned with the manufacturer’s needs.
Step 4: Implementing a Scalable Recruitment Process
To meet the aggressive hiring goals, Eastridge implemented a scalable recruitment process designed to handle high volumes of applicants. This process included:
- Streamlined candidate screening: Eastridge used an efficient pre-screening process to quickly assess candidates’ qualifications and fit for the role.
- On-site interviews and assessments: Candidates were brought in for interviews and technical assessments to ensure they had the skills needed for the job.
- Rapid onboarding: Once candidates were selected, Eastridge facilitated a fast-tracked onboarding process, ensuring new hires were quickly integrated into the production line.
The recruitment process was designed to move quickly while maintaining a high standard of candidate quality. This allowed the manufacturer to bring on employees in waves, ensuring that production targets were met without overwhelming the company’s internal resources.
Step 5: Managing Workforce Performance
Once the new employees were hired and onboarded, Eastridge continued to support the manufacturer by managing workforce performance and addressing any issues that arose. This included:
- Regular check-ins with supervisors: Eastridge maintained close communication with the manufacturer’s production supervisors to ensure that the new hires were meeting performance expectations.
- Ongoing support for employees: Eastridge provided support to the new hires, addressing any concerns they had and helping them integrate smoothly into the company culture.
- Performance tracking: Eastridge used metrics to track employee performance and identify areas for improvement, ensuring that the workforce continued to meet the company’s production goals.
This level of support helped the manufacturer maintain a high level of productivity while ensuring that new employees felt supported and engaged in their roles.
Results: A Rapidly Scaled Workforce and Production Success
Thanks to Eastridge’s strategic approach to workforce planning, recruitment, and management, the manufacturer was able to meet its goal of hiring 300 employees within the required timeframe. The results were clear:
- Production targets met: With the new workforce in place, the manufacturer was able to meet its production targets on time, ensuring that demand was met without delays.
- High-quality hires: Eastridge’s focus on screening, the GATE program assessments, and interviews ensured that the new employees had the technical skills needed to perform well in their roles, reducing the risk of operational disruptions.
- Employee retention: The strong support provided by Eastridge helped improve employee retention, with new hires staying on the job longer and contributing to the company’s success.
The manufacturer’s leadership team was particularly impressed by the seamlessness of the process. By partnering with Eastridge, they were able to focus on their core business while Eastridge handled the heavy lifting of recruitment, onboarding, and workforce management.
Conclusion: A Blueprint for Scaling Workforce in Manufacturing
For manufacturers facing the challenge of rapidly scaling production, having the right workforce partner is essential. Eastridge’s ability to plan strategically, recruit efficiently, and manage workforce performance allowed this manufacturer to meet its ambitious hiring goals and achieve production success.
This case study highlights the importance of having a flexible, scalable recruitment solution in place to address the unique demands of the manufacturing industry. Whether a company needs to ramp up quickly to meet demand spikes or maintain a steady pipeline of talent, Eastridge offers the expertise and resources to ensure success.