Proactive Solutions to Overcome the Manufacturing Talent Shortage
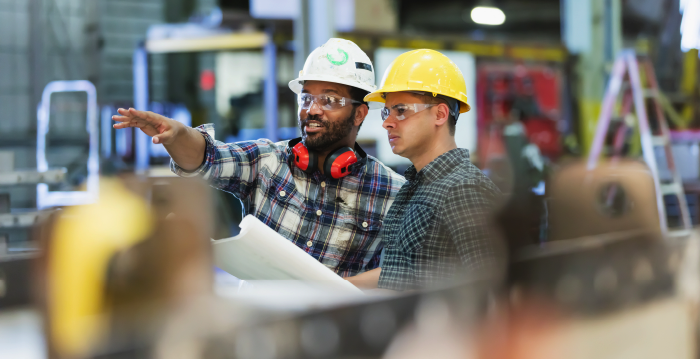
The manufacturing sector is experiencing an unprecedented talent shortage, driven by the retirement of experienced workers, rapid industry growth, and a misalignment between education and industry needs. By 2033, the industry will require 3.8 million new employees, but without significant changes, half of these positions may go unfilled. To address this challenge, manufacturing leaders must adopt proactive solutions focused on attracting, training, and retaining talent.
Understanding the Talent Shortage
According to a report by Deloitte, the skills gap in manufacturing could result in 2.1 million unfilled jobs by 2030.
Several key factors contribute to the talent shortage in manufacturing, including:
- Retirement of Experienced Workers: The aging workforce, particularly the retirement of Baby Boomers, is creating a significant gap.
- Industry Growth: Increased demand due to reshoring manufacturing operations and government incentives like the CHIPS Act.
- Educational Misalignment: Traditional education systems are not sufficiently preparing students for careers in manufacturing.
Strategic Solutions for the Talent Shortage
To effectively address these challenges, industry leaders must implement proactive and innovative strategies.
1. Investment in Training and Education
Organizations must prioritize training programs that equip workers with the necessary skills for modern manufacturing roles. Partnering with local trade schools and creating apprenticeship programs can be highly effective. Some programs help to identify an aptitude for manufacturing even when candidates have no prior experience.
For example, Eastridge’s GATE (Gateway to Achieving Talent Excellence) program is one model that provides in-person training and testing to ensure candidates possess essential skills such as basic math, manual dexterity, and an understanding of good manufacturing practices.
2. Upskilling and Reskilling
Upskilling current employees to take on more advanced roles and reskilling workers from other industries can help fill the talent gap. Cross-training within organizations ensures that employees can handle various tasks, making the workforce more flexible and efficient. This approach not only addresses immediate staffing needs but also fosters long-term employee retention by providing career growth opportunities.
Many times, Eastridge will work with clients to recruit a temporary pool of talent that can then selectively move into permanent positions after acquiring skills and experience.
3. Expanding Pools of Talent
Traditional recruitment methods may no longer be sufficient. Staffing partners play a crucial role in this regard. By leveraging their expertise and consultative approach, they help organizations identify candidates with transferable skills, even if they lack direct experience in manufacturing. For instance, workers from the fast-food industry, who have experience operating machines and assembling products, can be excellent candidates for manufacturing roles. As mentioned earlier, programs like GATE can be crucial in identifying candidates with an aptitude for manufacturing even though they lack the experience. We’ve also worked with clients to help preview a manufacturing environment with candidates who may have never experienced a manufacturing environment. This helps expand pools of talent but also reduces turnover.
4. Competitive Compensation and Benefits
Attracting new talent requires offering competitive wages and benefits. Pay rate inflation for manufacturing has averaged 5% annually. According to Indeed, while wage growth in manufacturing improved during the pandemic, wage growth in manufacturing has been slower compared to other industries, highlighting the need for competitive compensation to attract and retain talent.
However, wages aren’t the only lever to pull when it comes to compensation. For example, Eastridge will often work with clients to target recruiting areas leveraging detailed wage analysis to attract candidates. Expanding the talent pool (referenced earlier) can also help mitigate wage inflation by recruiting workers with less experience - in many cases introducing them to a higher wage and/or career path that generally pays more.
Additionally, offering flexible work arrangements, such as varied shift hours or partnerships for child care, can make manufacturing jobs more attractive to a broader range of candidates.
5. Creating a Positive Work Environment
Retention is as critical as recruitment. Providing continuous development opportunities, recognizing and rewarding employee contributions, and fostering a supportive work culture are essential strategies for retaining talent. Eastridge’s approach of integrating customer success managers to facilitate communication and address concerns is an effective way to maintain high levels of employee satisfaction and retention. Often the customer success team will uncover issues that are simple to solve, but can make a big difference for workers on certain shifts.
Conclusion
The manufacturing industry’s talent shortage is a complex challenge that requires a multifaceted approach. By investing in training and education, upskilling and reskilling, enhancing recruitment strategies, offering competitive compensation, and fostering a positive work environment, industry leaders can bridge the talent gap. With the right strategic partnerships and initiatives, organizations can achieve successful talent acquisition and retention, ultimately driving the manufacturing sector forward.
Read more about how Eastridge Industrial Staffing is helping clients get the most out of their workforce.